In this article:
1. What is Engineer-to-Order Manufacturing?
2. Advantages and disadvantages of Engineer-to-Order process?
3. Make-to-Order vs Engineer-to-Order
4. Real-World Examples of Engineer-to-Order
Today’s manufacturers need to be agile, so they can adjust to an evolving global marketplace with changing customer expectations and increasingly diverse, and often specific, demands. Meeting these specialized needs requires manufacturers to embrace an efficient and effective production strategy, like engineer-to-order (ETO) manufacturing.
This guide explains ETO manufacturing. It compares ETO to make-to-order manufacturing. It also discusses the advantages and disadvantages of ETO. Finally, it provides some real-world examples.
What is Engineer-to-Order Manufacturing?
ETO manufacturing is a customer-driven manufacturing process that produces unique solutions.
Unlike stocked products, ETO products are made to meet specific customer needs. They go through careful engineering and design planning before manufacturing starts.
Though the time, energy, and skill involved in creating ETO products may seem cost prohibitive, producing complex, specialized goods allows manufacturers to demand higher prices and gain a competitive advantage in the marketplace.
The process flow for ETO manufacturing can change based on the industry and company. However, there are some basic steps that all ETO manufacturers follow:
- Customer request and analysis: The customer introduces their product needs to the manufacturer, who uses this time to gather requirements and offer considerations.
- Preliminary design: The manufacturer creates a preliminary design that fits the customer’s specifications.
- Detailed engineering: Once the preliminary design is approved, the manufacturer’s engineering team creates a detailed design, which includes drawings, models, and specifications.
- Production planning and procurement: Production planning, including the procurement of materials and components needed, is the next step.
- Manufacturing and assembly: When all plans are in place and resources are procured, manufacturing commences, and the product is fully assembled.
- Testing: It’s critical that the product is tested rigorously, ensuring that it adheres to the detailed requirements and meets quality assurance standards before being delivered to the customer.
- Delivery, installation, and review: The finished product is delivered to the customer and installed. If the customer and manufacturer agree, the customer can check the product. This check is for accuracy and quality. It happens during the review phase.
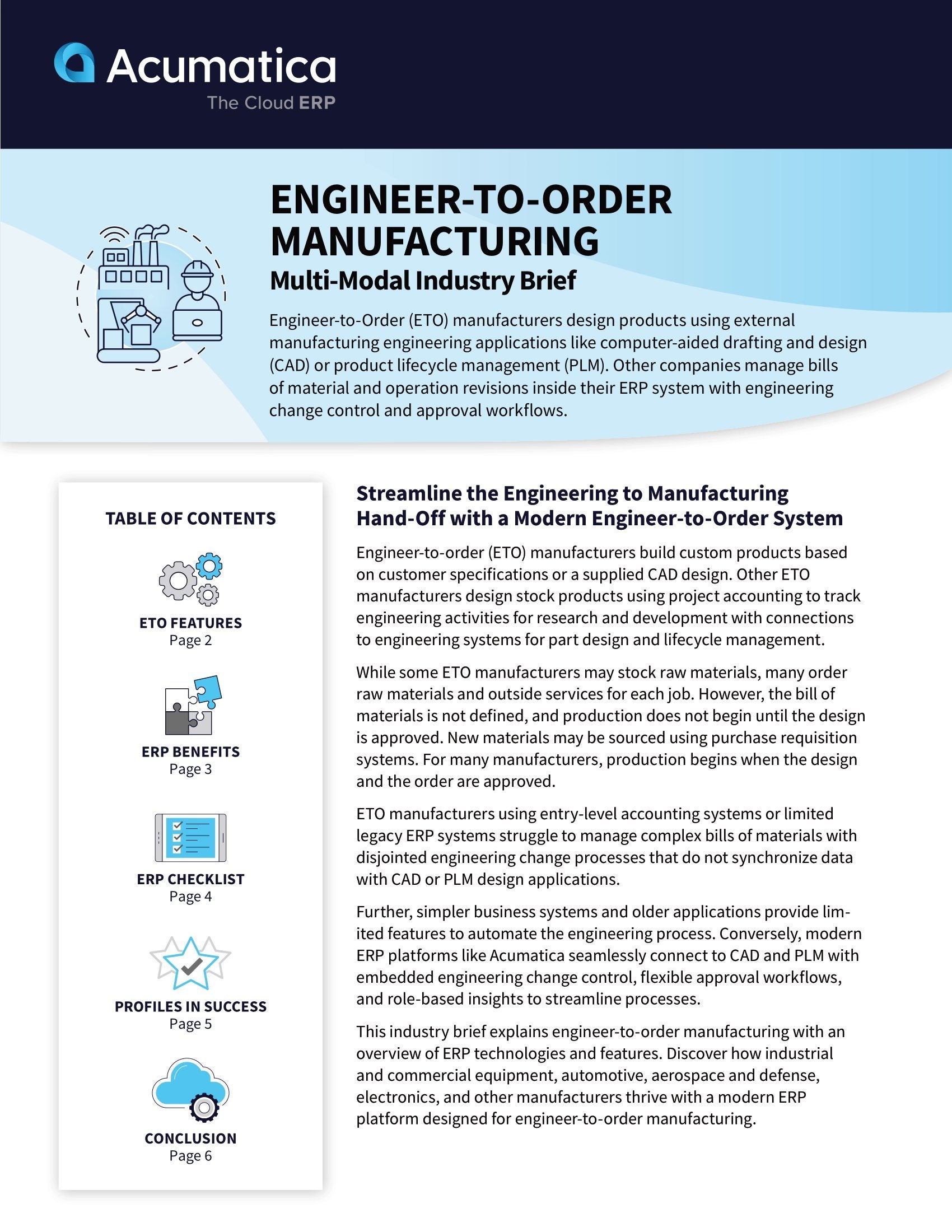
Engineer-to-Order: Advantages and Disadvantages
There are a number of advantages that come with ETO manufacturing, including higher potential profits, efficient production, fewer errors, and increased customer satisfaction. But such specialized manufacturing processes create a few disadvantages as well.
Examples include longer lead times for designing, planning, and building; higher costs revolving around customization and the potential need to develop new systems; and reduced scalability due to building unique products for a single customer rather than for mass production.
Make-to-Order vs Engineer-to-Order
Like engineer-to-order, make-to-order (MTO) is a widely used manufacturing process. MTO manufacturing begins with a customer’s order, but, unlike ETO, MTO customizes a pre-specified design.
Consider the customer who is in the market for a luxury car. The customer starts with a basic car. They can change some details based on the manufacturer. These details include the engine, interior, exterior, and entertainment system.
A perfect example is BMW. The German automaker allows customers to design their “ultimate driving machine,” starting with selecting the series and following the steps—including color, wheel type, and upholstery—until the final price is quoted.
Both MTO and ETO are customizable and flexible in nature, but only ETO manufacturing allows customers to be a part of the design process from the get-go.
Real-World Examples of Engineer-to-Order
In the construction industry, ETO is common for custom builds. Building a unique structure begins with the initial vision. This vision comes to life during the design process, which includes extensive engineering and customizations. Once the plan is approved, the materials are sourced, and the construction commences—a one-of-a-kind building is on its way to standing tall.
The aerospace industry also uses ETO manufacturing. Boeing and Airbus, the world’s biggest manufacturers of large commercial passenger aircraft, take detailed orders from airlines, working with them to design a product that fulfills their specialized requests. The planes are crafted from beginning to end based on the customer’s avionic, exterior, and interior expectations.
For the medical industry, specialized equipment and devices are often required. Customers in this industry choose ETO manufacturers because they offer flexibility and customization. They trust that the final products will meet their needs.
And the HVAC industry offers ETO manufacturing examples, as well. Some manufacturers design custom HVAC systems, like Acumatica customer Q-PAC Systems, Inc.
Q-PAC makes Plug-and-Play fan systems used in commercial HVAC systems for air handling retrofits and OEMs. The systems are designed based on customer specifications and can be found in office buildings, universities, airports, hospitals, and entertainment venues.
Though Q-PAC had its own ordering system named QUIPS, the company was managing production and costs and tracking inventory with QuickBooks and Excel spreadsheets. The team struggled to track the status of orders, quote projects, process engineering changes, assemble bills of materials, forecast, and more.
The disconnected, inefficient systems caused frustration, so Q-PAC sought a cloud-based enterprise resource planning (ERP) solution that could connect to QUIPS, offered multi-region support, was scalable, and allowed them to customize unique processes.
After Q-PAC evaluated several top-tier options, including Microsoft Dynamics, Odoo, Oracle NetSuite, and Acumatica, Acumatica’s unlimited-user pricing, open APIs, ease-of-use, flexibility, and seamless integration with third-party applications clinched the deal. Q-PAC implemented Acumatica Manufacturing Edition, gaining a number of key benefits in the process, including:
- Instant—anytime, anywhere—access to a single record of information.
- Real-time reporting.
- Seamless connection between QUIPS and Acumatica Manufacturing, allowing engineering, manufacturing, shipping, and invoicing data to flow between the two applications.
- Visibility into inventory and production costs.
- Faster production and improved revision history access through Bill of Materials functionality.
Q-PAC now imports its design specs from QUIPS directly into Acumatica, which automates the process of creating the manufacturing requirements and work orders for the subassemblies that ultimately roll up into a final assembly. Acumatica provides visibility, so everyone sees whether components are in stock and what capacity is needed for a project. Acumatica allows Q-PAC to see accurate inventory and production costs, which allows executives to calculate the project profitability correctly.
Conclusion
ETO manufacturing is a highly specialized approach that offers expansive engineering and customization to customers with unique product needs. Manufacturers who choose this option can get ahead of their competitors. They can deliver the exact product that customers want. This ensures customer satisfaction, which builds loyalty and increases profits.